Originally published on fastradius.com on August 12, 2020
What do car tires, watertight gaskets, shoe soles, rubber bands, and pencil erasers all have in common? Many of these objects are things we interact with on a daily basis, but they’re also made using elastomers, or “elastic polymers.”
Elastomeric materials are pliable synthetic polymers that are similar to rubber. While the two share similar characteristics, they differ in a few key ways. Rubber, for instance, is a naturally occurring compound derived from latex. While an incredibly useful and versatile material, rubber’s chemical makeup imposes certain manufacturing limitations and also makes parts prone to ozone cracking. Elastomers, on the other hand, are a family of petroleum-based polymers that act very similarly to rubber but offer better material properties.
This article will provide a brief primer on manufacturing with elastomeric materials.
Defining characteristics and mechanical properties of elastomers
Elastomers are materials that have the ability to stretch and then rebound back to their original shape. Elastomers provide a range of other benefits, including high elasticity, abrasion and tear resistance, impermeability, soft textures, and slip resistance. They can also withstand significant temperature fluctuations and are ideal for temperature and electrical insulation.
Elastomers can be chemically tuned for a broad range of applications. For example, elastomeric materials could be tuned for improved rebound for something like a shoe sole or tuned for a low rebound, dampening product like a grip. They can also provide suction and sealing. Depending on the application, selecting the right material can improve the desired characteristics of the final part.
Thermoplastics vs. thermosets
It’s important to note that there are two primary kinds of elastomers: thermoplastics and thermosets. Thermoplastics liquify when heated and solidify when cooled — a process that can be repeated, extending the lifecycle of the material. This quality makes them especially useful for manufacturing injection-molded parts at high volume. These strong polymer materials are typically shrink-resistant, shock-absorbent, and largely recyclable, as well.
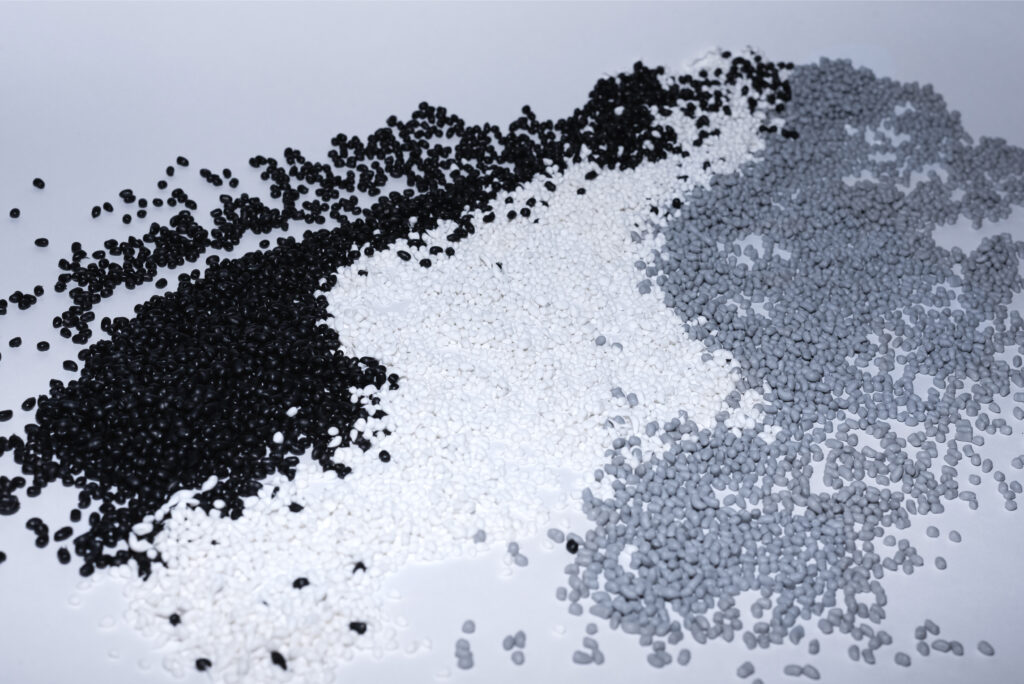
In contrast, thermoset plastics cannot be melted down and reused after the part has set. The curing process triggers a chemical reaction that incites the formation of incredibly strong three-dimensional cross-links between molecules within the polymer — the bonds are nearly impossible to break, even under extreme temperatures. Because of the high durability, strength, and warp resistance these bonds provide, thermosets are often used to reinforce other materials against impact and deformation.
Four important factors for designing and manufacturing elastomeric parts
In order to maximize the desired material properties of elastomeric parts, there are a few critical considerations that product teams would do well to keep in mind.
1. Lead with clearly-defined requirements
The specific requirements for a given application should drive material selection and design for the part. By having a clear understanding of those requirements, manufacturers can quickly determine which elastomeric material offers the most significant benefits.
Using a material requirements planning (MRP) system often proves beneficial for product teams. Working retroactively from production plans and schedules, these systems generate lists of component and material requirements that provide visibility into what materials are needed, in what quantity, and in what timeframe — all of which can help manufacturers stay on-schedule and properly resourced.
2. Achieve appropriate draft
Draft refers to tapered angles incorporated into part design that help ensure that the part is ejected smoothly from the mold. Insufficient draft not only makes the part harder to remove, but can also result in bends, breaks, warps, and inferior surface finishes as the plastic cools.
Elastomeric components typically require a significant amount of draft to prevent the material from sticking to the mold itself. Adding texture to the ejector pins to give them extra grip is another method for increasing the efficiency of removing parts from their molds.
3. Calibrate wall thickness to specific requirements
Generally, the thickness of a part’s walls should be kept between 1.5 and 3 mm of thickness and should be as uniform as possible. This helps the part cool faster (thereby reducing cycle time), and prevents irregular shrinkage and unsightly sink marks. If a part application requires varying wall thicknesses, then a gradual transition should be incorporated to maintain design integrity.
The pliable nature of elastomeric materials allows parts to be designed with higher wall thickness as well as variations in wall thickness. By applying pressure during production, engineers can shape or form the material in ways that cannot be achieved through injection molding or when manufacturing with more rigid materials.
4. Maximize effectiveness of overmolding
Overmolding refers to the process of creating an elastomer layer that is then attached to a rigid, non-elastomeric part. One common example of this is the pliable grip found on many hand tools, which provides slip resistance and keeps the user from holding onto rigid plastic or metal — both of which improve the safety and efficiency of the tool.
To maximize the effectiveness of an overmolded grip, engineers need to design the product to enable good bond strength between the elastomeric and rigid materials through both chemical and mechanical methods. The chemical attachment in particular is important because the bonds that form between the two materials improve the durability and longevity of the part, while also removing the need for additional surface pre-treatments or adhesives.
Efficient elastomer manufacturing — and more
Elastomers are a versatile category of rubber-like thermoplastics that offer significantly improved material qualities. Thermoplastic elastomers’ unique set of chemical and physical resistances — as well as their high pliability and strength — enable manufacturers to produce many of the items we interact with everyday, including everything from bicycle inner tubes to wetsuits.
Partnering with an experienced manufacturing partner like SyBridge Technologies empowers product teams to get the most out of any material or part design. Our team of experienced, collaborative engineers and designers are as adept at talking elastomer prototyping as they are the latest processes in additive manufacturing, and we work closely with each customer to ensure that every stage of the production process is optimized for specific design, manufacturability, and timeline requirements. Contact us today and discover the attention to detail, efficiency, and cost effectiveness that SyBridge Technologies brings.