Originally published on fastradius.com on August 26, 2020
Injection molding is a useful method of production that gives manufacturers the ability to create identical parts in high volumes with consistent quality and characteristics. During production, a pressurized nozzle shoots molten plastic into a durable metal mold designed to let the part cool and be ejected quickly. Once the part is ejected, the press closes and the operation repeats itself. Many everyday plastic items — from combs and bottle caps to car parts and gears — are produced through injection molding.
Historically, injection-molded parts had to be manufactured in large quantities in order to offset high startup costs. A hardened steel mold costs tens of thousands of dollars and can take weeks or months to tool, but over time, its durability allows manufacturers to recoup their investment while also lowering cost-per-part.
However, as markets evolve — evidenced, for example, by the ongoing shift toward custom and small batch products — manufacturers are adapting their operations to take advantage of new, more efficient methods. Low-volume injection molding is one of those methods.
Key benefits of low-volume injection molding
The process of low-volume injection molding eschews hardened steel molds and inserts for softer aluminum ones, which are typically easier and cheaper to make. These molds obviously aren’t as durable as their hardened steel counterparts, but the advantage for manufacturers is that they often don’t need to be when producing parts in low volumes. When used strategically, soft molds can ultimately reduce tooling costs and shorten production schedules.
Typically, low-volume injection molding refers to making parts in quantities of 100,000 or fewer. While that number probably seems high to a layperson, it’s still relatively low compared to high-volume production numbers, which can easily reach tens of millions of parts. While 100,000 isn’t an official cutoff, it serves as a general benchmark for the point at which aluminum molds become less cost-effective than investing in hardened steel molds.
At the same time, hardened steel required for traditional molds demands a significant upfront investment of time and money. However, aluminum and lower-grade steel molds are far less expensive to create and can be produced faster. With these molds, manufacturers can prototype and produce viable parts without having to commit to high minimum orders, while continuing to refine part design and production as needed. This allows manufacturers to begin production sooner, and in many cases, accelerate speed-to-market significantly, thereby reducing the time it takes to see a return on investment.
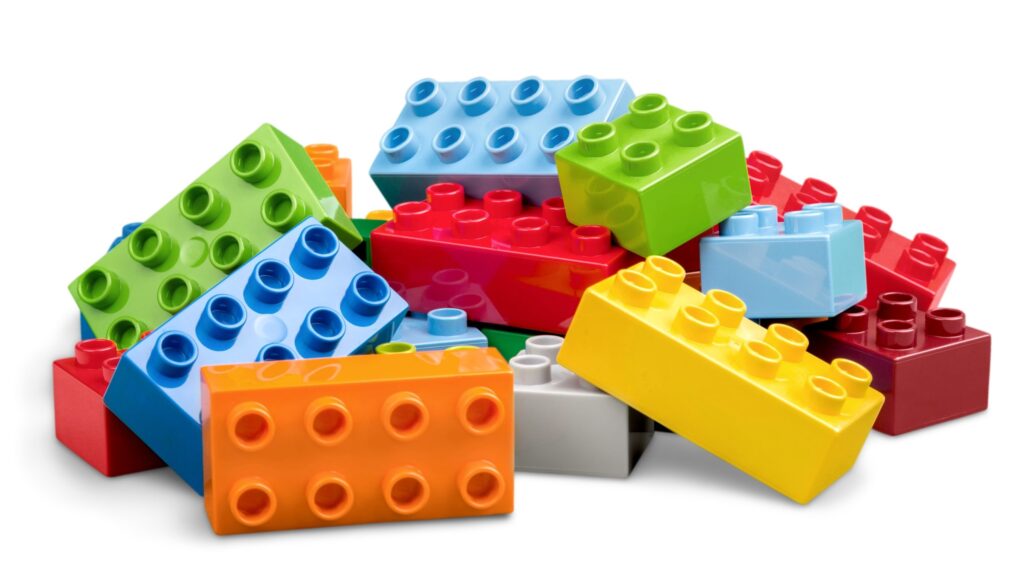
Shorter lead times are especially beneficial for smaller product teams on tight budgets, who can now produce parts with relatively low minimum orders while still turning a profit. Furthermore, storing and disposing of excess inventory can quickly become expensive, but low-volume rapid injection molding helps to minimize excess by enabling production teams to manufacture parts only in the quantities required.
In addition to creating opportunities for creating small-batch or custom parts, the rapid injection molding process provides an efficient means of bridge tooling. This allows manufacturing companies to begin tooling hardened steel molds while simultaneously employing aluminum molds to produce parts in the meantime.
Another significant benefit of employing softer injection molds is that they rarely have a detrimental effect on part quality: plastic pieces produced in low volumes are as good as those created via hardened steel molds when proper design considerations are taken into account.
Key design considerations for low-volume injection molding
There are a few important considerations that need to be kept in mind when designing parts for manufacturability at low volumes, including general part complexity, draft, wall thickness, and surface finish.
Typically when you work with aluminum, you do not want to implement side actions or lifters normally associated with complex builds into the tool. While those operations typically cause wear in the tool — softer aluminums cannot withstand such pressure for very long — low-hardness steels like P20 serve as optimal replacement tooling materials.
Draft refers to a taper incorporated into design that makes it easier for a part to be ejected from its mold. Consider a rectangular baking pan — if the pan were truly rectangular, it would prove difficult to remove a cake. However, rounded edges and tapered sides incorporated into the design of the pan allow the cake to easily emerge. This is a principle that holds true when removing injection-molded parts from their molds, as well. All vertical faces should have at least 0.5 degrees of draft, though closer to 2 or 3 degrees is preferable if part design allows. Some complex surfaces may require as many as 5 degrees of draft.
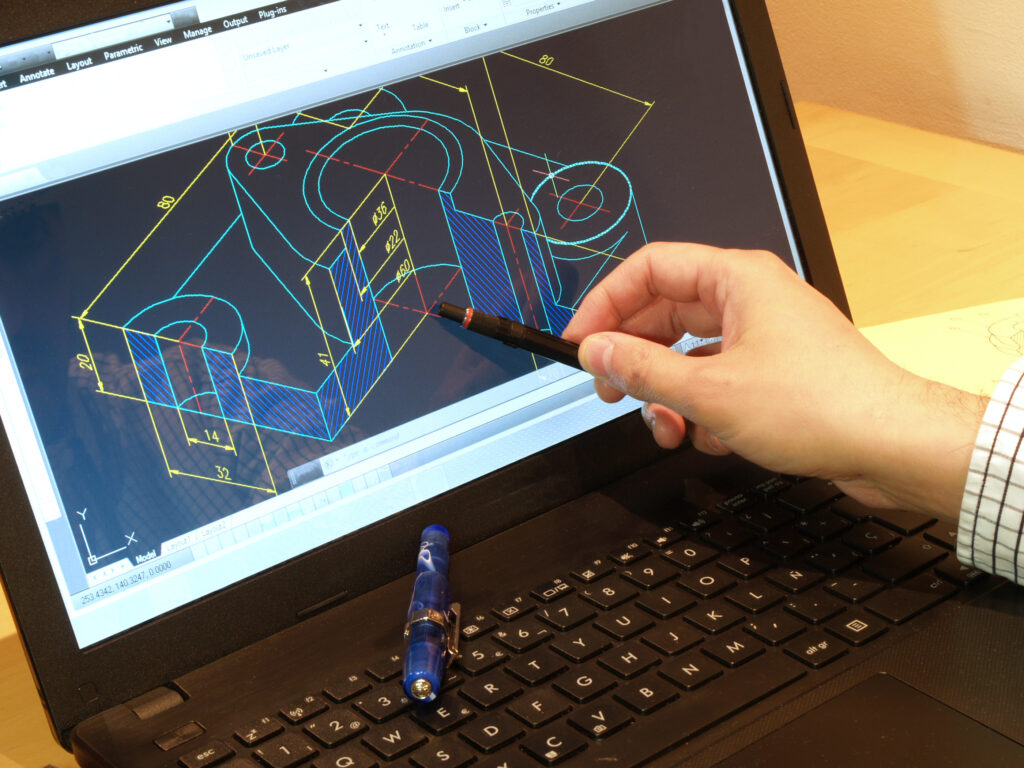
The thickness of a component’s walls also needs to be considered, as thicker walls don’t necessarily equate to greater strength or performance — especially when working with thermoplastic materials. Thick cross-sections actually increase the likelihood of parts developing warp or sink during the cooling process, which is why wall thicknesses should typically stay between 0.040 to 0.140 inches (1 to 3.5 millimeters) across the part’s entirety.
Manufacturers can also save on tooling costs and lead time by forgoing unnecessary surface finishes to their molds. If the part’s application does not require an extremely smooth surface — which can involve hand-polishing mold cavities with diamond buffs — there’s probably no need to have it. Using the most cost-efficient finish compatible with a given part’s application is key to lowering production costs and improving production times.
Using low-volume injection molding to your advantage
Injection molding is an incredibly useful manufacturing method often leveraged to create large numbers of identical parts. The high cost of tooling the hardened metal molds means that the parts must be produced at high volumes in order for the project to prove cost-effective. However, developments in manufacturing processes and technology now enable product teams to economically create rapid injection-molded parts in smaller quantities and to provide efficient bridge tooling solutions.
At SyBridge, we’re always striving to do our jobs more efficiently. That means working closely with each of our customers — from design and prototyping through to post-production and fulfillment — to ensure that they receive high-quality parts that are made affordably and delivered on short timelines. Contact us today to discover how we can make your designs come to life.