This article originally appeared on nTopology’s blog. Published on fastradius.com on November 2, 2020.
3D printing has enabled production of complex structures not previously achievable through conventional manufacturing processes. nTop is pioneering a new era of CAD software that can keep up with these advances, allowing designers to generate incredibly complex geometry quickly and easily.
We have noticed that when customers have limited additive manufacturing experience, their minds are constrained by the limitations of traditional manufacturing methods like injection molding and CNC machining. While each additive process also has inherent limitations, we aim to push ourselves and our customers to think beyond conventional design wisdom to drive functional and aesthetic innovation afforded by increased design freedom.
This can be illustrated through an internal design challenge my team had to create a sneaker that could be printed as one part using an elastomeric material on HP’s Multi-Jet Fusion technology. Our design workflow demonstrates how nTop can be a playground for industrial design exploration. We were able to quickly generate a wide breadth of design options for the various components of a shoe — the tongue, shoe upper, midsole, and sole — and try out different design permutations in a matter of minutes as opposed to the hours or days it would take with traditional parametric or mesh-based CAD software.
nTop’s computational power
nTop’s computational power shines in its ability to quickly generate tailored lattice structures. In one shoe’s upper design, we used spherical fields to drive cell spacing for a voronoi lattice. This technique allows designers to have deep control over both the aesthetics and functionality of their products.
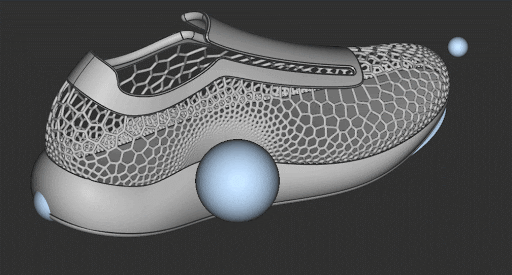
nTop’s block-based interface makes it easy to try out different lattice and TPMS structures in a given design space. You can define variables such as cell size and beam thickness to easily edit your lattice. Because blocks are independent of each other and not a linear model tree, you can run the same geometry through different functions and not worry about having to start from scratch if you change your mind later.
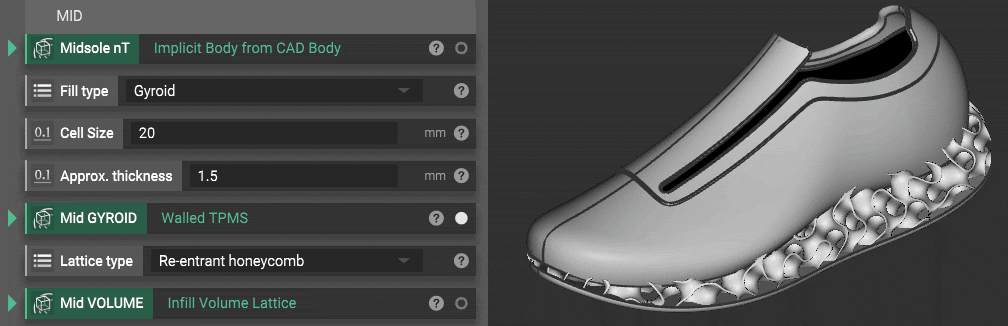
nTop is a data-driven software and we frequently make use of its properties blocks to get instant feedback on our design. For the shoe, we calculated a volume fraction of the TPMS structure over the total design space to get a sense of the density of the shoe midsole. This block informs us how subsequent parameter changes affect the stiffness of the midsole.
Going beyond lattices with nTop
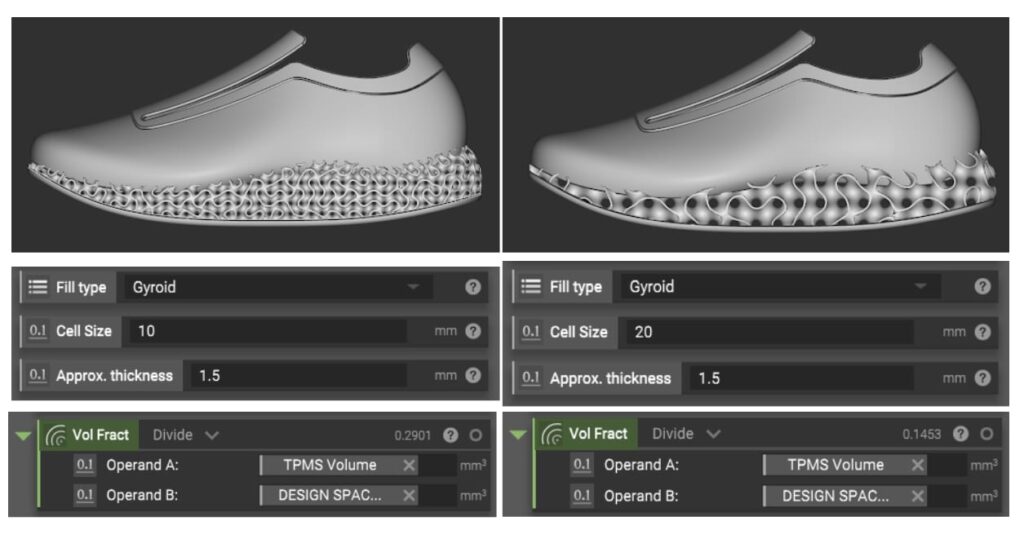
Beyond structural lattices, nTop has a variety of features that allow complex manipulation of surfaces. We used several different methods to explore texturing the shoe sole. We created treads and traction by combining blocks in nTop’s architected materials toolkit. A more advanced, custom texture was generated by mathematically manipulating the surface of the design space using our company logo.
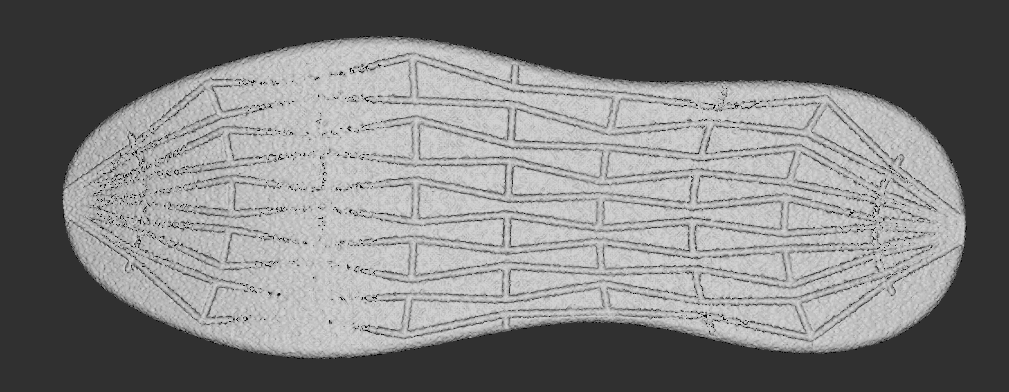
Once we generated a variety of options for each of the shoe components, we were able to toggle visibility on each of the components to visualize different design combinations. This is a game-changer for industrial designers who know the importance of rapid iteration and idea quantity to ultimately create a higher quality, more innovative final product.
Contact us to get started today.