Originally published on fastradius.com on November 3, 2021
Injection molding is a simple and repeatable process that’s ideal for mass-producing parts with intricate shapes. This process uses high heat and pressure to inject melted material into the injection mold before cooling the material. After cooling, you can open the mold and reveal your finished part.
A well-made mold, or tool, is essential to producing functional injection-molded parts. As 3D-printing technology has developed, 3D-printed injection molds have become a cost-effective alternative to traditional steel tooling. Are 3D-printed molds the best choice for your next production run? Here’s what you need to know.
How 3D-printed injection molds are made
To 3D print injection molds, you’ll need to create a digital file that’s the inverse of your final design. The printer will read the file and deposit material in layers accordingly, adding supports where needed to prevent deformation. Once printing is complete, the mold can be inserted into an aluminum frame that supports the mold against the heat and pressure of the injection molding nozzle to prevent warpage.
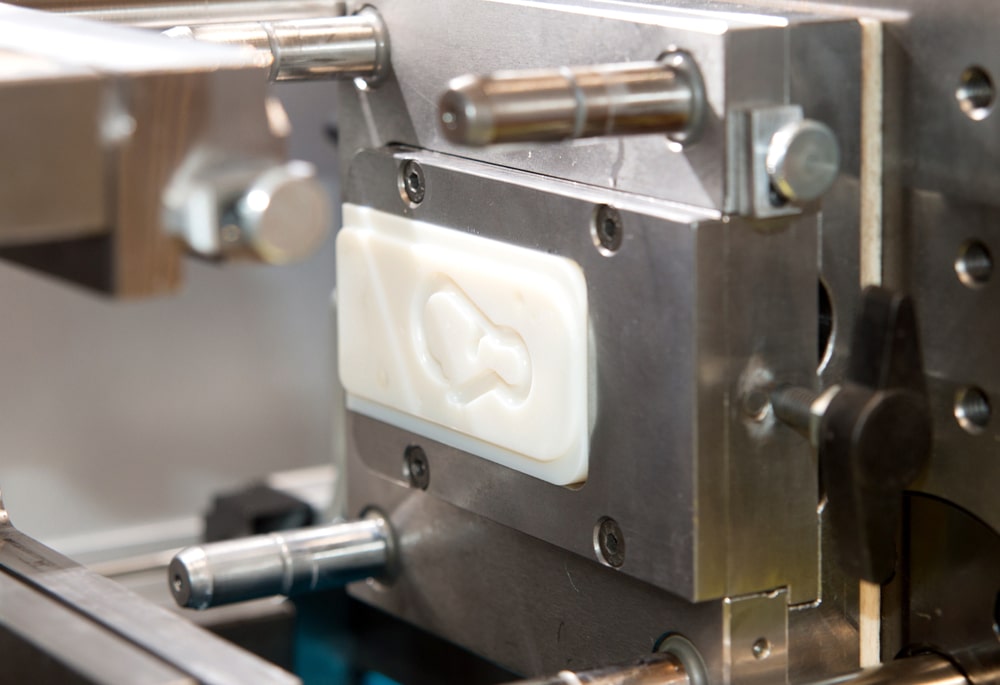
When designing a mold, include air vents in the design to improve the melted material’s flow into the mold, minimize pressure, speed up the injection process, and reduce the risk of flashing. You can also print the mold at a lower layer height and orient the mold’s inner faces so no support structures touch either face of the mold. This improves the surface quality of the part and minimizes the amount of post-processing needed.
The advantages of 3D-printing injection molds
3D printing is a great mold tooling option if you want to keep production costs low. The injection molding process in itself is very cost-effective for high-volume production runs, but making the molds can get expensive very quickly. Complex steel molds with multiple cavities, for example, can easily cost over $100,000. Many manufacturers have their injection molds 3D printed because it allows them to produce molds at a fraction of the cost of traditional methods and it makes low-volume production runs more cost-effective. Traditional mold tooling methods are expensive and require lots of equipment, but 3D printing simple injection molds requires limited equipment and can cost significantly less.
In addition to being cheaper, making molds with 3D printing is much faster than using traditional tooling methods. It may take two to five months to produce a steel injection mold and 10-15 days to fabricate an aluminum injection mold via CNC machining, but it typically takes just two to three days to create a 3D-printed mold. Using additive manufacturing processes involves no tooling and little to no manufacturing preparation, making it ideal for those looking to achieve fast turnaround times without sacrificing complexity or accuracy.
You can print accurate, complex components with a 3D printer. This high level of accuracy combined with lower costs also makes 3D printing great for quickly creating detailed prototypes that accurately represent the final product. Engineers can alter the design and see the results quickly, enabling them to refine the mold before mass production and reduce the likelihood of errors.
The limitations of 3D printing injection molds
3D printing injection molds offers plenty of advantages, but there are a few limitations to consider. For example, you can only 3D print a mold that’s around the size of a grapefruit because part volumes are often limited to 10 cubic inches. Building a mold using electrical discharge machining (EDM), on the other hand, allows you to create accurate mold cavities with part volumes of up to 59 cubic inches. Plus, since 3D printing deposits material layer-by-layer, a 3D-printed mold may have small edges on angled surfaces that require machining or sanding to remove.
Also, a 3D-printed mold is less durable than a traditionally tooled mold under certain circumstances. 3D-printed plastic molds tend to break down when they are continually exposed to the heat and pressure of injection molding, so they should only be used for prototyping or small runs of up to 1000 parts. For high-volume production runs, consider using CNC machining or EDM to create steel or aluminum molds for injection molding.
Partnering with SyBridge
3D printing has made creating injection molds fast and cost-effective, but it isn’t suitable for every situation. If you’re planning a large run or need to create large parts, you may be better off using a traditional tooling method, such as CNC machining or EDM. An experienced manufacturing partner can help ensure you choose the mold tooling method that will yield the best results for your project.
When you partner with SyBridge, our team of experts will help you determine if using 3D-printed injection molds is the best option for your project. When you take advantage of our injection molding services, you’ll receive strong, precise parts with excellent surface finishes at a low cost per unit. Contact us today to get started.